Research progress on comprehensive utilization of fluorine-containing solid waste in the lithium battery industry
Abstract
With the rapid development of the lithium-ion battery (LIB) industry, the inevitable generation of fluorine-containing solid waste (FCSW) during LIB production and recycling processes has drawn significant attention to the treatment and comprehensive utilization of such waste. This paper describes the sources of FCSW in the production of LIBs and the disposal of spent LIBs. Subsequently, the fundamental characteristics of FCSW were introduced, including resource properties and hazardous attributes. Furthermore, it comprehensively reviews recent technologies for treating FCSW. Finally, future research on FCSW was prospected. This paper aims to provide practical guidance for the treatment and application of FCSW in the LIB industry, help solve the problem of resource recovery in HCSW treatment, and promote the HCSW industry to achieve more efficient and sustainable development.
Keywords
INTRODUCTION
The world faces significant challenges, including resource scarcity, climate change, environmental pollution, and energy depletion[1]. The root cause of these challenges is humanity’s massive consumption of and heavy reliance on fossil energy[2]. The structure of the global energy system urgently needs to shift from the absolute dominance of fossil energy to a green, low-carbon, clean, efficient, smart, and diversified future[3]. As the clean energy lithium industry has become an important driver in the global energy sector, lithium-ion batteries (LIBs) have the characteristics of high energy, long life, cost-effective, less pollution[4-6], and are widely used in new energy vehicles, consumer electronics, energy storage power stations, and other fields[7,8]. With the blowout use of LIBs, the number of scrapped LIBs after the life cycle is exhausted is also increasing yearly, making them the fastest-growing solid waste in the world[9]. International Energy Agency (IEA)’s sustainable development scenario shows that the amount of LIBs spent will reach 1,336.5 GWh by 2040 [Figure 1][10]. However, it should be noted that the production and recycling process of LIBs may have environmental impacts[11,12], especially the fluorine-containing solid waste (FCSW) during the production and recycling process of lithium batteries, which is increasingly becoming a bottleneck that cannot be ignored in the development of the industry.
FCSW, a by-product of LIB manufacturing and recycling processes, has potential environmental toxicity and long-term persistence, leading to significant adverse environmental impacts. With the continuous growth in demand for LIBs, effectively managing and utilizing FCSW has become an urgent requirement for the sustainable development of the lithium battery industry. Therefore, addressing this issue is paramount for reducing environmental burdens and promoting a circular economy.
Research has been conducted in recent years on the comprehensive utilization of FCSW. Various explorations, ranging from fluoride recovery to resource utilization to value-added waste, have been proposed and explored to maximize the utilization and resourcefulness of this waste, thereby reducing environmental pressure and enhancing industrial sustainability. However, there has been no review of the comprehensive utilization of FCSW in the LIB industry. Herein, we comprehensively investigated the pathways of FCSW generation during the production and recycling processes of LIBs. Secondly, the essential characteristics of FCSW are described, including resourcefulness and hazardousness. We then detail the current treatment and disposal methods of FCSW, concluding with an overview of the future challenges facing fluorinated solid waste. This review will provide a reference for advancing the research on FCSW.
SOURCES OF FCSW IN THE LITHIUM BATTERY INDUSTRY
FCSW from lithium battery production processes
The main components of native lithium ore are silicates, along with elements such as fluorine, tantalum, niobium, tin, aluminum, cesium, and potassium[13,14]. Fluorine accounts for approximately 1%-15% of the lithium ore content[15-18] in the form of lithium fluoride and fluorine lithium compounds. Fluorides may be released during the extraction and processing of lithium ore, forming FCSW. The process of lithium extraction is mainly divided into acid, alkali, salt roasting, and chlorination methods[19,20].
The sulfuric acid method is widely used for extracting lithium from ores. It is currently the only industrial method for lithium extraction, including roasting, acid roasting, leaching, purification, evaporation, lithium precipitation, and anhydrous sodium sulfate concentration crystallization [Figure 2][21]. Lithium extraction using the sulfuric acid method needs to be carried out at high temperatures. The fluorine-containing waste gas generated in the treatment process is usually absorbed by CaO or Ca(OH)2, producing a large amount of FCSW[22].
The alkali method is used to extract lithium, reducing the energy consumption and high cost of the sulfuric acid method. Hydrothermal alkali treatment converts α-spodumene into hydroxy sodalite, and lithium in the ore is released into solution and then precipitated for recovery [Figure 3][23]. The fluorine in lithium marble does not produce highly corrosive hydrofluoric acid in an alkaline environment, avoiding equipment corrosion, but fluorine still exists in the generated slag to form FCSW.
Metal ions in the sulfate (such as potassium sulfate, sodium sulfate, and calcium sulfate) occupy the structural positions of lithium ions in the ore, separating lithium ions from the insoluble aluminum silicate and forming soluble sulfate[23]. The salt roasting method has low impurity content, high leaching rate, good comprehensive recovery of metals, and a simple process. It has also been widely used in the industrial production of lithium extraction from lithium mica. The sulfate process also requires high-temperature roasting, during which the fume containing fluorine and sulfur is volatilized and collected with sodium hydroxide to produce FCSW [Figure 4][24,25].
The chlorination process uses a chlorination agent to transform precious metals such as lithium in ore into chloride for extraction[26]. The main chlorinating agents are NH4Cl, NaCl, and CaCl2[27]. Zhu et al. reported that lithium chloride was volatilized at 1,000 °C after mixing lithium spodumene, calcium chloride, and limestone[28]. The resulting lithium chloride was collected and washed, and lithium carbonate was obtained by precipitating lithium carbonate solution [Figure 5]. Zhang et al. used a chlorination agent mixture of CaCl2 and NaCl, and the extraction efficiency of Li reached 92.49% under the best conditions[29]. The mixture of CaCl2 and NaCl reduces the melting temperature and promotes the chlorination reaction, during which fluorine is converted to CaF2 into the waste residue to produce FCSW.
In conclusion, the primary techniques for lithium extraction from lithium ores currently include the sulfuric acid method, alkali method, sulfate method, and chlorination roasting method. Each method has its own advantages and disadvantages [Table 1], and it is necessary to strengthen the research on the process of extracting lithium from ores, develop corresponding technologies, simplify process steps, and save energy. However, due to the presence of fluoride resources in lithium ore, any technological method used to extract lithium will produce fluorine-containing flue gas or FCSW.
The advantages and disadvantages of lithium extraction technology
Treatments | Advantages | Disadvantages |
Sulfuric acid method | Mainstream process, widely used, mature technology | High temperature, large energy consumption, produce fluorine waste gas |
Alkali method | Reduces chemical raw materials and energy, and decreases emissions of sulfur and chlorine | The defluorination gas is difficult to treat |
Salt roasting method | Low cost, less corrosion to equipment | More energy, large material flow and high reaction temperature |
Chlorination method | Short process, high lithium recovery rate, less residue | Equipment corrosion, high equipment requirements, difficulty utilization of leached residue |
During the preparation of the positive electrode material for LIBs, HF is used for etching and cleaning, generating a large amount of fluorine-containing wastewater. In preparing the harmful electrode material for LIBs, fluorine-containing electrolytes generate fluorine-containing wastewater during production. According to statistics, every ton of LiF crystals produced will produce about five tons of fluorine-containing wastewater[30]. Current treatment methods for fluorine-containing wastewater include precipitation treatment[31], adsorption techniques[32], ion exchange methods[33], and membrane treatment processes[34]. Adsorption and ion exchange methods have a high selectivity for the target ions; however, in polyanionic solutions, due to the low degree of separation by competitive adsorption[35,36], membrane treatment processes have high operating costs[37]. Therefore, the precipitation method is mainly used in industrial processes to treat fluorine-containing wastewater at a low price and with high efficiency. Calcium salt is the most commonly used defluorination agent, which generates CaF2 precipitate by adding limestone[38], thereby separating fluoride ions in water and producing a large amount of FCSW.
FCSW from lithium battery recycling processes
The LIB recycling process has four stages: classification, stabilization, disassembly and separation, and treatment[39,40]. Classification is based on the condition, chemical composition, shape, size, and health status of batteries to establish rational processes for disassembly. Dedicated containers store and promptly handle batteries exhibiting leakage, smoking, electrical leakage, shell damage, etc.
The residual charge of the battery during disassembly of used LIBs may release a large amount of heat, causing spontaneous combustion or explosion[41,42]. Therefore, the LIBs must be discharged before removing the battery casing to reduce the risk of spontaneous combustion or short circuit. LIBs are usually placed in a conductive aqueous solution to release the residual charge. The most commonly used conductive solution is NaCl[43], and some fluoride ions are dissolved in the NaCl solution. Acidic and alkaline dissolved discharges are more rapid[43]. Still, they can damage the battery case, causing electrolyte leakage and reacting with the surrounding water, producing toxic HF dissolved in the conductive solution. Discharge of LIBs in aqueous solutions of calcium salts has also been studied, with the calcium salts directly precipitating dissolved fluoride ions[44]. In any case, aqueous fluorine-containing solutions or FCSW are formed during the discharge process.
After discharge, the battery is dismantled, disassembled, and crushed to separate its materials and components. Although different manufacturers produce the components or quantities of LIBs, the electrolyte and electrode materials in the discarded LIBs contain fluorine chemicals, such as binders and electrolytes[45]. Polyvinylidene fluoride (PVDF) has a strong and stable carbon-fluorine unit structure (-CH2-CF2-) and is a non-polar structure with multiple chain conformations[46]. Typically, PVDF is semi-crystalline, comprising both crystalline and amorphous regions, which not only provide mechanical strength but also facilitate the diffusion and retention of electrolytes[47]. These properties confer PVDF with high electrochemical stability, excellent bonding capability, and the ability to absorb electrolytes effectively. Consequently, PVDF facilitates the efficient transfer of lithium ions to active materials, making it a widely used primary component in binders for LIBs[48]. This material is insoluble in water, and its dissolution typically requires the use of an organic solvent such as N-Methyl-2-pyrrolidone (NMP); in this process, PVDF decomposition and solvent phase separation result in the release of HF into the organic medium[49]. In addition, fluorine-containing adhesives such as PVDF can also be removed by high-temperature pyrolysis (> 400 °C), which produces toxic gases such as HF in the decomposition process and needs to be absorbed by alkali, resulting in a large amount of FCSW[50].
The electrolyte comprises an organic solvent and lithium fluoride salt solution[51]. The organic solvent is a mixture of ethylene carbonate (EC), propylene carbonate (PC), diethyl carbonate (DEC), dimethyl carbonate (DMC), and ethyl methyl carbonate (EMC) in different proportions[52]. Lithium salts include LiPF6, LiBF4, and LiClO4[53]; LiPF6 readily reacts with air and water to produce HF, which volatilizes into the air or dissolves in water to produce fluorine-containing wastewater.
After the electrolyte is physically extracted during dismantling and crushing, it needs to be recycled. Methods include thermal decomposition, solvent extraction, alkaline absorption, and freezing[54].
Tang-treated waste LiCoO2 combined pyrolysis and hydrometallurgical leaching, and the organic component electrolyte and binder were recovered as pyrolysis oil and gas. In the pyrolysis gas, fluorine was converted into hydrogen fluoride and absorbed with a saturated Ca(OH)2 solution to produce FCSW[55].
The solvent extraction method is to add appropriate organic solvents in the electrode material; the electrolyte will be transferred to the organic solvent, and the different boiling points of the components in the extraction solution will be used for distillation, separation, and collection of organic solvents and electrolytes[56]. Zhu et al. immersed waste lib in DMC solution; the electrolyte was dissolved and mixed with NaOH solution. After filtration, the aqueous phase was added to the calcium nitrate solution, and fluorine was converted to CaF2 and precipitated into FCSW[57]. The main reactions occurred as
The researchers[58] first used DMC extraction to recover the electrolyte from the waste lib and then separate it by vacuum distillation; separate DMC is used for recycling extraction of another waste electrolyte. After separation, the waste electrolyte is removed with water, which affects the performance of the electrolyte phosphate ester, and LiPF6 is converted into LiF to recover lithium. The oil phase (organic solvent) is then separated from the water phase, Ca(OH)2 is added to the water phase, and F is recovered as CaF2 in FCSW.
The alkaline absorption method uses an alkaline solution to treat the acidic electrolyte. Mao et al. treated the spent electrolyte with Ca(OH)2, which produced a large amount of FCSW residue containing CaF2[54]. The freezing method first cools the residual electrolyte with liquid nitrogen, crushes, heats, evaporation, and then recovers with NaOH or KOH solution, which converts the fluoride ions in the spent electrolyte into stable fluoride salts[59]. Li et al. used liquid nitrogen to freeze the residual electrolyte in the battery to avoid the hydrolysis reaction of LiPF6 with water vapor to produce hydrogen fluoride gas[60]. Subsequently, a mixed aqueous solution of sodium hydroxide and calcium hydroxide is added to absorb the spent electrolyte solution, and the fluorine is converted into CaF2 precipitate into the FCSW residue.
Although efforts to recycle components such as binders and electrolytes in waste LIBs are increasing, the complete recycling of each component from spent LIBs remains elusive. In future research, it is necessary to further optimize the energy consumption of existing processes to achieve both economic benefits and environmental protection. For example, environmentally friendly solvents could be selected to replace traditional organic solvents for dissolving binders, more efficient freezing methods could be developed, and the use of microorganisms or enzymes to degrade electrolytes could be explored to minimize environmental impact.
After the waste LIBs have been pre-treated, valuable materials can be recovered in various ways, such as through pyrometallurgy, hydrometallurgy, or direct recovery. The waste lithium anode material contains a lot of valuable metals, such as Co, Ni, Li, Mn, etc., and the negative electrode material is mainly graphite[61]. Recycling used lithium-ion secondary batteries can alleviate the shortage of metal resources and contribute to environmental protection. The negative electrode material of waste LIBs is usually treated by a hydrometallurgical process[62,63]. Inorganic and organic acid reagents are often used to extract valuable metals from the active material of the cathode[44]. In the hydrometallurgical process pretreatment, the organic binders in the battery anode material (mainly PVDF) and electrolyte (mainly LiPF6) are not entirely separated from the battery system, and the fluorine compounds enter the acid-leaching solution with the waste anode material, resulting in a large amount of fluorine-containing wastewater[64]. Xu et al. used poly-aluminum sulfate to defluorination from nickel-manganese mixed H2SO4 leach solution of spent LIBs[65]. Under the optimal conditions of Al to F molar ratio = 2, pH = 5.5, temperature 60 °C, reaction time 30 min, and stirring speed 500 r/min, the concentration of fluoride ions ranged from 1,205 to 48 mg/L, and 96% of the fluorine could be precipitated. In this process, fluorine is converted to AlF3, AlF(OH)2, and LiAlF4; a large amount of FCSW is generated. Similarly, treating fluorinated wastewater from the LIB recycling process generates much FCSW.
In recent years, processes that are simple, cost-effective, highly efficient in recovery, and environmentally friendly have increasingly gained favor. Xiao et al. reported a method for extracting valuable metals from LIBs using ultrasonic-assisted citric acid leaching, which reduced leaching time by 50% and achieved an average metal ion recovery rate of 97% ± 3%[66]. Esmaeili et al. studied the use of ultrasonic-assisted citric acid and H2O2 for leaching LIBs, with optimal conditions leading to 100% recovery of Li, Co, and Ni within 35 min[67]. While ultrasonic-assisted organic acids effectively recover valuable metals from LIBs, fluorides remain in the waste residue, forming FCSW.
CHARACTERISTICS OF FCSW PRODUCED IN THE LITHIUM BATTERY INDUSTRY
Chemical constitution
The chemical composition of FCSW can vary significantly depending on its source and the processes involved. However, some standard components found in such waste may include: Fluorides: Compounds containing the fluoride ion, such as NaF, MgF2, CaF2, or HF. Fluorosilicates: Compounds containing fluorine and silicon, such as Na2SiF6. Depending on the specific materials being processed or disposed of, some fluorine-containing waste may also contain trace metals such as Al, Fe, and Ca. Depending on the source of the waste, other contaminants such as heavy metals, organic solvents, or other hazardous chemicals may be present.
Preciousness
The chemical diversity of FCSW enhances its resource richness and increases its potential for recycling and reuse. As a result, FCSW contains a variety of materials that can be effectively recycled or repurposed. Depending on the source and composition of the waste, the most prominent are various fluorine compounds such as NaF, CaF2, MgF2, Na3AlF6, and fluorosilicates. With the rapid development of the fluorine chemical industry, using FCSW as a source of fluorine resources is urgent and significant. In addition, FCSW may contain other metals, such as aluminum, magnesium, or calcium, which can be recycled through recovery or extraction processes. Part of FCSW may have a high calorific value, making it suitable for energy recovery through incineration or pyrolysis, which can produce heat or electricity and provide a pathway for the waste to be used as a resource. It must be noted that the feasibility and efficiency of recovering these resources from FCSW depend on various factors, including waste composition, existing technologies, economic viability, and environmental considerations. The goal is to maximize the recovery of resources and minimize the impact on the environment.
Perniciousness
The discussion of the preciousness of FCSW highlights its significant potential as a valuable resource; however, it is also essential to consider its harmful aspects. While the fluorides and other compounds in FCSW offer valuable opportunities for recycling and energy recovery, improper management can lead to the excessive accumulation of fluorides in the environment, which severely affects the health of individuals, plants, and animals. Figure 6 illustrates the harmful effects of fluorides on animals, plants, and humans.
Harmful for plants
FCSW contains a significant amount of fluorine elements, and prolonged storage may result in the emission of fluorine-containing gases into the air. Fluorine compounds in FCSW may enter water bodies through surface runoff or seepage when it rains and cause water pollution, which may have toxic effects on aquatic organisms and aquatic plants, damaging aquatic ecosystems and affecting water quality and the sustainable use of water resources. When rainwater containing fluoride ions penetrates the soil, the deposition of fluoride ions affects soil parameters, causing an increase in pH and influencing the activity of soil microbial communities, ultimately leading to soil degradation[68,69]. High levels of fluoride ions can affect vegetation-related processes, including photosynthesis, respiration, protein synthesis, glucose metabolism, and nucleotide synthesis[70]. The detrimental effects of fluoride ions on plants primarily manifest in reduced photosynthetic efficiency, decreased enzyme activity, metabolic disturbances, disruption of plant structural integrity, and potentially leading to plant necrosis[71].
Harmful for animals
Animals consuming plants contaminated with fluorides and frequently inhaling fluorine (gas and dust) will exhibit evident symptoms and diseases of dental fluorosis[72]. The primary indications of the chronic condition investigated extensively in cattle by Suttie et al. include abnormal teeth development, medullary lesions, and diminished appetite, leading to weight loss or decreased milk production[73]. Fluoride can induce oxidative stress, alter intracellular redox balance, elevate protein carbonyl levels and lipid peroxidation, modulate gene expression, and initiate apoptosis[70]. Based on the work by Giri et al., fluoride has been found to modulate genes related to the physiological stress response, cell cycle regulation enzymes, intercellular interaction, and signal transmission pathways[74].
Harmful for human
Fluoride is listed as one of the twelve most hazardous pollutants by the United States Agency for Toxic Substances and Disease Registry due to its high reactivity and toxicity[75]. It is an essential nutrient for humans and animals. Still, excessive exposure can be harmful, and ingestion of fluoride above optimal levels [> 1.5 mg/L, World Health Organization (WHO), 2011] can lead to severe dental and skeletal fluorosis in humans[76-79]. Fluoride can replace calcium content in teeth and bones, weakening them and eventually leading to osteoporosis, especially in adults and the elderly[80]. The impact of fluoride on health is chronic, with prolonged exposure to high doses of fluoride having adverse effects on human health. Recent research reports indicate that elevated levels of fluoride intake can have detrimental effects on health, leading to hypertension[81], neural defects, nervous system damage, genetic harm, and damage to the kidneys, liver, and thyroid. They may even lead to cancer-causing diseases of the lungs, bones, bladder, and uterus[82-84].
TREATMENT TECHNOLOGY
Landfill
Part of FCSW is left exposed in the open air without treatment, while other portions are landfilled after solidification/stabilization[85,86]. However, landfilling is not a thorough treatment method. On the one hand, occupying land resources extensively due to the large volume of FCSW leads to widespread soil contamination as harmful substances directly permeate the soil under various natural influences. On the other hand, during heavy precipitation, pollutants may seep into the burial site, and with water flow, contaminants can permeate out and enter water systems through surface runoff. Due to the high mobility and convergence of water resources, it is very easy for these pollutants to spread to water resources in various parts of the region, which will have a significant impact on flora and fauna in the waters and may even cause a large number of deaths of aquatic organisms, affecting the water quality situation, and resulting in a further reduction of freshwater resources.
Chemical method
The chemical treatment methods for FCSW can be divided into pyrometallurgical, hydrometallurgical, and combined pyrometallurgical-hydrometallurgical processes.
Pyrometallurgy
Pyrometallurgy treats solid waste through high-temperature processes, usually smelting or roasting, to recover valuable materials or reduce the waste’s hazardous nature. The treatment process is simple, easy to operate, adaptable, and efficient[87,88]. Figure 7 shows the specific steps of pyrometallurgical treatment of FCSW.
Yang et al. carried out experiments on direct-roasted FCSW[89]. At 1,200 °C, a significant amount of NaF could be effectively removed. Further roasting enabled completely removing NaF, Na3AlF6, AlF3, and
Zhu et al. used the Box-Behnken design (BBD) to investigate the effects of particle size, roasting temperature, and time on the fluorine removal efficiency from FCSW[90]. The results showed that all of them had a significant effect on the fluorine removal effect. Fluorine removal was 88% under the optimized conditions of the process (temperature of 1,499 °C, time of 3.33 h, average particle size of 10 mm), and CaF2 was detected to remain in the FCSW without being completely removed.
In recent years, significant efforts have been made to solve the problems of long processing time and low fluoride removal efficiency in the traditional high-temperature roasting FCSW fluoride removal process. Microwave heating is characterized by comprehensive and uniform heat distribution, rapid temperature elevation, high efficiency, and energy conservation[91,92]. Zhu et al. used microwave-assisted high-temperature roasting technology to treat FCSW, which was crushed to 1-3 cm and then put into high-temperature microwave equipment for reaction[93]. NaOH solution absorbed the waste gas. The results show that the fluoride removal efficiency of the traditional and microwave roasting methods was 80% and 93.7%, respectively, after roasting at 1,400 °C for 2 h. Compared to the traditional roasting process, the content of CaF2 and Na3AlF6 in the microwave roasting process decreased by 0.37% and 3.90%, indicating that microwave-assisted roasting is more effective in removing fluoride. Microwave high temperature roasting at 1,500 °C for 2 h reaction can achieve a fluoride removal rate of 95.4%. The substances encapsulated outside the fluoride are broken during microwave high-temperature roasting, causing the fluoride to volatilize.
To reduce the roasting temperature, Dong et al. used sulfuric acid as an additive for co-roasting, and investigated the effects of sulfuric acid dosage, roasting temperature, and time on the fluorine conversion efficiency, and 99.4% of the fluorine could be converted to HF under the optimal conditions [m(H2SO4)/m(FCSW) of 1.4:1, 360 °C, 2 h][94]. The decomposition of the fluorine component in FCSW during the reaction process can be expressed as Equations (3-8). The NaOH solution is used to absorb the flue gas.
The pyrometallurgical process for treating FCSW is simple and effective, but faces challenges such as high energy consumption and long processing times, especially the problem that CaF2 in FCSW is difficult to volatilize, which requires higher temperatures for effective removal. Microwave-assisted roasting, as an emerging technology, not only improves fluorine removal efficiency but also significantly reduces processing time, offering great potential for application. However, the equipment cost and energy consumption of microwave technology still require further optimization. Additionally, additive-assisted roasting has shown the potential for efficiently converting fluorides at lower temperatures, but further investigation is needed into its effects on equipment corrosion and flue gas treatment. Future research should focus on reducing energy consumption while improving fluorine removal efficiency, ensuring the economic viability and environmental sustainability of the process.
Hydrometallurgy
The method of hydrometallurgy is to contact solid waste with water, acid, alkali, and other solutions, transfer the target elements in the raw material to the liquid phase through a chemical reaction, and obtain valuable components after separation and enrichment to achieve the treatment and disposal of solid waste[95]. This process consumes relatively little energy and has low production costs, in addition to the advantages of simple operation and easy-scale production[96]. The specific steps of hydrometallurgical treatment of FCSW are shown in Figure 8.
Lisbona et al. broke the waste to 1.18 mm and removed soluble NaF through water washing[97]. The washed residue reacts in an Al(NO3)3·9H2O solution at 25 °C for 24 h, and the total fluoride leaching efficiency after two-stage washing ranges from 76% to 86%. Some insoluble Na3AlF6 and CaF2 remain in the reaction residue. Lisbona et al. further improved the leaching method and used a mixed Al(NO3)3·9H2O and HNO3 solution to leach the slag washed to remove NaF[98]. The effect of Al3+, initial acid concentration, temperature, residence time, solid-to-liquid ratios, and particle size on the leaching efficiency was studied. 96.3 wt.% of insoluble fluoride (Na3AlF6 and CaF2) was leached under optimum conditions (0.36 mol/L Al3+, 0.5 mol/L HNO3, 60 °C, 4 h). The leaching efficiency was significantly higher than leaching with a single Al(NO3)3·9H2O solution. This is primarily because, in the absence of HNO3, hydrated aluminum hydroxyl fluoride precipitates on the solid residue, leading to a reduction in fluoride extraction efficiency. By combining the experimental results with a solution equilibrium mathematical model, it was determined that AlF2+ and AlF2+ are the primary species responsible for fluoride extraction from Na3AlF6 and CaF2. The dissolution process is expressed as
Wu et al. developed an aluminum salt solution leaching process to recover fluorine from FCSW[99]. At an
Nie et al. used a two-stage water-acid leaching process to leach soluble and insoluble fluorine from waste[100]. Under the optimum conditions, which were determined to be 0.20 mol/L Fe3+, 0.48 mol/L initial H+, the liquid-solid ratio of 10 mL/g, 30 min, and 80 °C, the extraction percentage of fluoride reached 88.5%. Extraction of insoluble fluoride from acidic Fe3+ solutions is achieved by complex leaching with the following Equations (20) and (21). The leaching process of insoluble fluorine in acidic Fe3+ solutions is controlled by interfacial transfer and interlayer diffusion of products with an activation energy of 38.2 kJ/mol. The unrecovered fluorides remain in the leaching residue in the form of CaF2.
Hydrometallurgy treatment of FCSW offers advantages such as low energy consumption, low cost, and simple operation, enabling efficient fluoride removal under relatively mild conditions. In particular, the leaching efficiency of insoluble fluoride is improved by introducing the synergistic effect of aluminum salt and nitric acid. Future research should focus on optimizing reaction conditions to further enhance fluoride removal efficiency while reducing acid consumption and energy usage, as well as controlling the generation of by-products during the process. Additionally, exploring the resource utilization of the treated residue to prevent secondary environmental pollution is another critical issue to address.
Pyro-hydrometallurgical process
Research has indicated that the combined use of pyrometallurgy and hydrometallurgy, making full use of their respective characteristics, can achieve more efficient resource recovery, reduce energy consumption and environmental impact in the waste treatment process, and enhance the sustainability of waste treatment. The specific steps of Pyro-hydrometallurgical treatment of FCSW are shown in Figure 9.
Tao et al. combined the acidification-roasting process for effective recovery of F from FCSW, using Al2O3 as a catalyst, and roasting experiments were carried out after the acidification of FCSW, Al2O3, and H2SO4[101]. Increasing the roasting time and acid-to-material ratio are beneficial for enhancing fluorine extraction. Under the conditions of 275 °C and 5 doses of H2SO4, the optimum F extraction efficiency (99.76%) was realized by roasting for 4 h with 1 dose of Al2O3 as the catalyst. In the absence of Al2O3, some H is consumed to form NaHSO4, resulting in a decrease in the binding of H with F, and the produced AlF3 cannot react with acid [Equation (22)], leaving F stored in the residue. The main product of roasting is NaAl(SO4)2 under the condition of Al2O3 presence, with no residual AlF3. F binds well with H, and the extraction efficiency of F increases from 80.76 to 99.76%.
Yao et al. constructed a preliminary technical route for processing FCSW through mechanochemical activation, molten salt roasting, water leaching, carbonate decomposition, evaporation crystallization, and multi-stage filtration techniques[102]. This method converts insoluble fluorides in FCSW into soluble fluorides that can be removed by roasting with Na2CO3 [Equations (23) and (24)]. The results showed that the optimal parameters of mass ratio (Na2CO3:FCSW) of 1.25:1, the heating efficiency of 3.75 °C/min to
Yao et al. further strengthened the roasting process using a NaOH-Na2CO3 mixed molten salt system and investigated the effects of NaOH-to-Na2CO3 mass ratio, mixed alkali-to-FCSW mass ratio, roasting temperature, and time on the leaching efficiency of fluorine[103]. After mechanical activation (250 rpm, ball-to-material ratio of 6:1, 4 h), with a NaOH-to-Na2CO3 mass ratio of 1:4 and a mixed alkali-to-FCSW mass ratio of 1:1, roasting at 900 °C for 180 min resulted in 97.35% of the fluoride transferring to the water leaching solution. No characteristic peak of CaF2 was detected in the leaching residue, and fluoride
The combined pyrometallurgical and hydrometallurgical process significantly enhances fluoride recovery efficiency in the treatment of FCSW, while also reducing environmental impact. The effective integration of multiple techniques strengthens the modularity of the process, providing strong support for the recovery of complex components FCSW. Future research should focus on optimizing these methods to achieve more efficient fluoride removal, reduce processing costs, minimize energy consumption, and improve the economic viability and environmental sustainability of the process.
In summary, there are various methods for fluoride treatment, including landfill, pyrometallurgy, and hydrometallurgy. Each has its own advantages and disadvantages in terms of treatment efficiency, cost, energy consumption, and environmental impact [Table 2]. Therefore, it is necessary to comprehensively consider these factors in selecting an appropriate method for the treatment of FCSW.
Advantages and disadvantages of FCSW treatment methods
Treatments | Advantages | Disadvantages |
Landfill | Simple and straightforward, no complex equipment or technology | Incomplete treatment, occupy land resources, cause soil and water pollution |
Pyrometallurgy | Simple process, easy operation, high adaptability and efficiency | High energy consumption and high cost |
Hydrometallurgy | Low energy consumption, low cost, simple operation, easy to scale production | Limited removal efficiency, residual fluorides remaining |
Pyro-hydrometal-lurgical process | Effectively recovers resources, reducing energy consumption and environmental impact | Complex process, higher operating technology and equipment investment |
Resource utilization of defluorinated residues
After FCSW undergoes defluorination treatment, it still contains many other elements, such as calcium, magnesium, and silicates. Recycling the defluorination residue can reduce its negative environmental impact and potentially recover its economic value.
For building materials
Fluorine is present mainly in CaF2 and MgF2 in FCSW. Defluorinated slag contains a large amount of Ca and Mg, which can be used as additives in building materials such as cement and concrete. Adding defluorinated slag as a mineralizer to raw cement materials for cement production can fix the remaining fluorine in the cement clinker at high temperatures and reduce the sintering temperature of the cement clinker. The defluorinated slag’s chemical composition and mineral phase are similar to Portland cement. Defluorinated slag can replace limestone to prepare Portland cement clinker. When the replacement amount is less than 30%, the sintering temperature of the clinker can be reduced, the setting time of cement can be shortened, and the compressive strength can be improved[104]. Gao et al. studied defluorinated slag as an auxiliary activator in sodium carbonate-activated slag cement. Ca2+ released in the dissolved slag promoted calcium-containing products’ formation, improved cement’s compressive strength, and reduced CO2 emissions[105]. In addition to cement binder alternatives, studies have shown that defluorinated slag has been used as a cementing material to partially or entirely replace Portland cement[106,107].
For ceramics
The defluorinated slag can provide Ca and Mg sources to prepare ceramics, and the ceramics can fix fluorine ions. Zhu et al. used waste serpentine tailings, waste Kaolin, and defluorination slag as raw materials to prepare ceramics[108]. The results showed that the two-stage heating method could avoid the generation of HF in the firing process, and fluorine in the defluorination slag could replace oxygen to form a SiOxF4-x tetrahedral structure, with compressive strength reaching 154 MPa. The leaching toxicity test showed that fluorine would not be released into the solution, and the ceramic produced by defluorinated residue was feasible. It would not cause harm to the environment. Zhu et al. used low-temperature sintering technology to prepare ceramics with sodium borate, sodium phosphate, and waste alumina as raw materials[109,110]. In the sintering process, fluoride removal slag was added. The toxicity leaching and corrosion resistance tests proved that fluorine curing in the inert crystal phase would hardly cause environmental pollution due to secondary release.
These methods for the resource utilization of detoxified residues not only reduce environmental burden but also offer certain economic value. On the one hand, defluorinated slag, as a substitute material, decreases dependence on natural resources and lowers production costs. On the other hand, its application in cement and ceramics helps mitigate the environmental impact of waste accumulation and reduces the secondary release of pollutants. Future research should focus on improving the utilization efficiency of defluorinated slag in practical applications and ensuring its long-term stability and safety.
CONCLUSIONS AND FUTURE DEVELOPMENT
Conclusions
The disposal of FCSW has become a barrier to the sustainable development of the FCSW industry in China because of the difficulty of fluoride conversion in FCSW. For the recovery of effective resources in FCSW, the existing methods are difficult to achieve industrial and large-scale disposal. The main reasons for limiting the recovery of FCSW include limited research, immature processing technology, and high cost. For example, the limited current research may be insufficient to establish a robust theoretical foundation for the effective resource recovery of FCSW. A lack of in-depth understanding of the mechanisms for efficiently and safely recovering fluorides and other valuable components hinders the selection of optimal technological pathways for resource recovery. The immature processing technology may lead to low recovery efficiencies, hindering the effective recovery of valuable resources from FCSW. Moreover, these technologies may fail to adequately manage safety concerns during the treatment process, such as the volatilization of fluorides or the formation of hazardous by-products, which can result in environmental pollution and pose significant health risks. High costs directly affect the economic viability of FCSW treatment and resource recovery. Elevated processing expenses may render resource recovery economically unfeasible, particularly in cases involving low-value waste. Costly technologies may only be economical if processed on a large scale or under specific conditions. This limits the application of these technologies in small and medium-sized enterprises or resource recovery facilities. Furthermore, the absence of standardized protocols governing FCSW disposal and subsequent product utilization exacerbates these challenges, profoundly impeding the effective handling and reutilization of FCSW materials.
Future development
Despite the considerable attention directed toward the reduction, treatment, and reuse of FCSW by researchers, several drawbacks persist. Integrating insights from the current research landscape of FCSW and considering market dynamics, we propose the following recommendations for FCSW disposal.
Process innovation based on efficient fluorine circulation and high-value fluoride products. At present, direct conversion and leaching processes are mostly used to recycle FCSW, and little consideration is given to the recycling and high-value utilization of fluorine resources. Future research should focus on integrating advanced separation and purification technologies to enhance the efficiency of fluorine recovery and utilization. For example, methods such as membrane separation, solvent extraction, or selective precipitation could be explored to isolate and obtain high-purity, high-value fluoride compounds. These compounds can be applied in specialized fields such as electronics, pharmaceuticals, and advanced materials manufacturing. Developing efficient fluorine recycling in FCSW recycling and the preparation of high-value fluoride products is the direction of future technological innovation.
Establish a technical system for the coordinated disposal of multi-source FCSW. FCSW has diversity because of its varying production processes, resulting in various fluorine-containing phases and fluorine content. The collaborative treatment of different FCSWs is the key future research direction of FCSW treatment. It is necessary to establish a sound, comprehensive utilization technology, use the commonality and individuality of different FCSWs for effective collaborative treatment, promote the maximum utilization of resources, and ensure the realization of the dual goals of environmental safety and sustainable development. For example, researching advanced characterization techniques to rapidly identify and quantify the different fluorine phases and fluorine content in FCSW will facilitate the design of customized treatment processes tailored to specific types of waste. This approach will ensure more efficient and effective resource recovery.
Establish a circular economy performance evaluation system for multi-source FCSW. The multi-dimensional and all-round coupling mechanism of energy consumption, environment and economic benefits involved in recycling multi-source FCSW is crucial to its development. Therefore, future research should develop a systematic evaluation framework of “technical solution-product-economic benefit-energy efficiency-environmental policy”. This framework will enable a comprehensive assessment of the recycling processes, ensuring that the technologies employed are not only economically viable but also environmentally sustainable and energy-efficient. By establishing this evaluation system, resource recovery can be optimized, environmental footprints minimized, and the overall sustainability of FCSW management practices improved. This approach will facilitate the transition to a circular economy, where waste is systematically converted into valuable resources, thereby achieving long-term environmental and economic objectives.
Enhancing government support for the healthy development of the FCSW Industry. The government should strengthen the formulation and improvement of relevant laws and regulations, enhance the establishment of toxicity identification and evaluation standards for FCSW, formulate disposal technical specifications for FCSW, and provide clear policy guidance and support for enterprises by proposing technical feasibility guidelines. Local governments can formulate and issue FCSW disposal standards in combination with regional economic and industrial structure planning, and establish special funds and tax incentives to support the development and implementation of FCSW emission reduction, treatment and reuse.
DECLARATIONS
Authors’ contributions
Conceived and designed the study and wrote the manuscript: Zhang X, Pan D
Drew the table and figure: Zhao H
Involved in analyzing the experimental data: Zhao H, Zhang X, Pan D
Availability of data and materials
Not applicable.
Financial support and sponsorship
This research was financially supported by the Young Elite Scientists Sponsorship Program by BAST (BYESS2023070).
Conflicts of interest
All authors declared that there are no conflicts of interest.
Ethical approval and consent to participate
Not applicable.
Consent for publication
Not applicable.
Copyright
© The Author(s) 2024.
REFERENCES
1. Kober T, Schiffer H, Densing M, Panos E. Global energy perspectives to 2060 - WEC’s world energy scenarios 2019. Energy Strateg Rev 2020;31:100523.
2. Cherubini F, Strømman AH. Life cycle assessment of bioenergy systems: state of the art and future challenges. Bioresour Technol 2011;102:437-51.
3. Zeng X, Li M, Abd El-Hady D, et al. Commercialization of lithium battery technologies for electric vehicles. Adv Energy Mater 2019;9:1900161.
4. Arshad F, Lin J, Manurkar N, et al. Life cycle assessment of lithium-ion batteries: a critical review. Resour Conserv Recy 2022;180:106164.
5. Alfaro-Algaba M, Ramirez FJ. Techno-economic and environmental disassembly planning of lithium-ion electric vehicle battery packs for remanufacturing. Resour Conserv Recy 2020;154:104461.
6. Zhang X, Li Z, Luo L, Fan Y, Du Z. A review on thermal management of lithium-ion batteries for electric vehicles. Energy 2022;238:121652.
7. Oryani B, Koo Y, Shafiee A, et al. Heterogeneous preferences for EVs: evidence from Iran. Renew Energ 2022;181:675-91.
8. Miao Y, Hynan P, von Jouanne A, Yokochi A. Current Li-ion battery technologies in electric vehicles and opportunities for advancements. Energies 2019;12:1074.
9. Pathak P, Srivastava RR, Ojasvi. Assessment of legislation and practices for the sustainable management of waste electrical and electronic equipment in India. Renew Sust Energ Rev 2017;78:220-32.
10. Li J, Li L, Yang R, Jiao J. Assessment of the lifecycle carbon emission and energy consumption of lithium-ion power batteries recycling: a systematic review and meta-analysis. J Energy Storage 2023;65:107306.
11. Harper G, Sommerville R, Kendrick E, et al. Recycling lithium-ion batteries from electric vehicles. Nature 2019;575:75-86.
12. Yang H, Hu X, Zhang G, et al. Life cycle assessment of secondary use and physical recycling of lithium-ion batteries retired from electric vehicles in China. Waste Manag 2024;178:168-75.
13. Beskin SM, Marin YB. Classification of granitic pegmatites and pegmatite-bearing granitic systems. Geol Ore Deposit 2018;60:578-86.
14. Kol’tsov VY, Yudina TB, Azarova YV, Semenov AA, Lizunov AV, Lesina IG. Comparative geological and mineral-petrological analysis of ore-bearing rock in lithium and beryllium deposits for modeling the behavior of ore minerals during processing. At Energy 2017;122:81-6.
15. Guo H, Kuang G, Li H, Pei W, Wang H. Enhanced lithium leaching from lepidolite in continuous tubular reactor using H2SO4+
16. Schneider A, Schmidt H, Meven M, et al. Lithium extraction from the mineral zinnwaldite: Part I: effect of thermal treatment on properties and structure of zinnwaldite. Miner Eng 2017;111:55-67.
17. Kuai Y, Yao W, Ma H, Liu M, Gao Y, Guo R. Recovery lithium and potassium from lepidolite via potash calcination-leaching process. Miner Eng 2021;160:106643.
18. Luong VT, Kang DJ, An JW, Dao DA, Kim MJ, Tran T. Iron sulphate roasting for extraction of lithium from lepidolite. Hydrometallurgy 2014;141:8-16.
19. Karrech A, Azadi M, Elchalakani M, Shahin M, Seibi A. A review on methods for liberating lithium from pegmatities. Miner Eng 2020;145:106085.
20. Li H, Eksteen J, Kuang G. Recovery of lithium from mineral resources: state-of-the-art and perspectives - a review. Hydrometallurgy 2019;189:105129.
21. Bishimbayeva G, Zhumabayeva D, Zhandayev N, et al. Technological improvement lithium recovery methods from primary resources. Orient J Chem 2018;34:2762-9.
22. Gmar S, Chagnes A. Recent advances on electrodialysis for the recovery of lithium from primary and secondary resources. Hydrometallurgy 2019;189:105124.
23. Gao T, Fan N, Chen W, Dai T. Lithium extraction from hard rock lithium ores (spodumene, lepidolite, zinnwaldite, petalite): technology, resources, environment and cost. China Geol 2023;6:137-53.
24. Guo H, Lv M, Kuang G, Wang H. Enhanced lithium extraction from α-spodumene with fluorine-based chemical method: a stepwise heat treatment for fluorine removal. Miner Eng 2021;174:107246.
25. Yan Q, Li X, Yin Z, et al. A novel process for extracting lithium from lepidolite. Hydrometallurgy 2012;121-4:54-9.
26. Yan Q, Li X, Wang Z, et al. Extraction of lithium from lepidolite using chlorination roasting-water leaching process. T Nonferr Metal Soc 2012;22:1753-9.
27. Barbosa L, Valente G, Orosco R, González J. Lithium extraction from β-spodumene through chlorination with chlorine gas. Miner Eng 2014;56:29-34.
28. Zhu ZH, Zhu CL, Wen XM, Zhu GQ, Ling BP. Progress in production process of lithium carbonate. Int J Salt Lake Res 2008;16:64-72. (in Chinese). Available from: http://ir.isl.ac.cn/handle/363002/861. [Last accessed on 24 Sep 2024]
29. Zhang X, Aldahri T, Tan X, Liu W, Zhang L, Tang S. Efficient co-extraction of lithium, rubidium, cesium and potassium from lepidolite by process intensification of chlorination roasting. Chem Eng Process 2020;147:107777.
30. Han Z, Wu S, Wu X, et al. Recycling of lithium and fluoride from LiF wastewater from LiF synthesis industry by solvent extraction. J Environ Chem Eng 2023;11:110557.
31. Liu C, Liu J. Coupled precipitation-ultrafiltration for treatment of high fluoride-content wastewater. J Taiwan Inst Chem E 2016;58:259-63.
32. Yang K, Li Y, Tian Z, Peng K, Lai Y. Removal of fluoride ions from ZnSO4 electrolyte by amorphous porous Al2O3 microfiber clusters: adsorption performance and mechanism. Hydrometallurgy 2020;197:105455.
33. Pan B, Xu J, Wu B, Li Z, Liu X. Enhanced removal of fluoride by polystyrene anion exchanger supported hydrous zirconium oxide nanoparticles. Environ Sci Technol 2013;47:9347-54.
34. Plattner J, Naidu G, Wintgens T, Vigneswaran S, Kazner C. Fluoride removal from groundwater using direct contact membrane distillation (DCMD) and vacuum enhanced DCMD (VEDCMD). Sep Purif Technol 2017;180:125-32.
35. Alhassan SI, Huang L, He Y, Yan L, Wu B, Wang H. Fluoride removal from water using alumina and aluminum-based composites: a comprehensive review of progress. Crit Rev Env Sci Tec 2021;51:2051-85.
36. Tao W, Zhong H, Pan X, Wang P, Wang H, Huang L. Removal of fluoride from wastewater solution using Ce-AlOOH with oxalic acid as modification. J Hazard Mater 2020;384:121373.
37. Nunes-Pereira J, Lima R, Choudhary G, et al. Highly efficient removal of fluoride from aqueous media through polymer composite membranes. Sep Purif Technol 2018;205:1-10.
38. Patel G, Pal U, Menon S. Removal of fluoride from aqueous solution by CaO nanoparticles. Sep Sci Technol 2009;44:2806-26.
39. Sommerville R, Shaw-stewart J, Goodship V, Rowson N, Kendrick E. A review of physical processes used in the safe recycling of lithium ion batteries. Sustain Mater Technol 2020;25:e00197.
40. Yu D, Huang Z, Makuza B, Guo X, Tian Q. Pretreatment options for the recycling of spent lithium-ion batteries: a comprehensive review. Miner Eng 2021;173:107218.
41. Rouhi H, Karola E, Serna-Guerrero R, Santasalo-Aarnio A. Voltage behavior in lithium-ion batteries after electrochemical discharge and its implications on the safety of recycling processes. J Energy Storage 2021;35:102323.
42. Wang Z, Yang H, Li Y, Wang G, Wang J. Thermal runaway and fire behaviors of large-scale lithium ion batteries with different heating methods. J Hazard Mater 2019;379:120730.
43. Shaw-Stewart J, Alvarez-Reguera A, Greszta A, et al. Aqueous solution discharge of cylindrical lithium-ion cells. Sustain Mater Technol 2019;22:e00110.
44. Chen H, Gu S, Guo Y, et al. Leaching of cathode materials from spent lithium-ion batteries by using a mixture of ascorbic acid and HNO3. Hydrometallurgy 2021;205:105746.
45. Qian Y, Hu S, Zou X, et al. How electrolyte additives work in Li-ion batteries. Energy Storage Mater 2019;20:208-15.
46. Kochervinskii VV. The structure and properties of block poly(vinylidene fluoride) and systems based on it. Russ Chem Rev 1996;65:865-913.
47. Zhivulin V, Pesin L, Belenkov E, Greshnyakov V, Zlobina N, Brzhezinskaya M. Ageing of chemically modified poly(vinylidene fluoride) film: evolution of triple carbon-carbon bonds infrared absorption. Polym Degrad Stabil 2020;172:109059.
48. Zhang Y, Zhang X, Zhu P, Li W, Zhang L. Defluorination and directional conversion to light fuel by lithium synergistic vacuum catalytic co-pyrolysis for electrolyte and polyvinylidene fluoride in spent lithium-ion batteries. J Hazard Mater 2023;460:132445.
49. Yao L, Feng Y, Xi G. A new method for the synthesis of LiNi1/3Co1/3Mn1/3O2 from waste lithium ion batteries. RSC Adv 2015;5:44107-14.
50. Lombardo G, Ebin B, Steenari B, Alemrajabi M, Karlsson I, Petranikova M. Comparison of the effects of incineration, vacuum pyrolysis and dynamic pyrolysis on the composition of NMC-lithium battery cathode-material production scraps and separation of the current collector. Resour Conserv Recy 2021;164:105142.
51. Kwabi DG, Ji Y, Aziz MJ. Electrolyte lifetime in aqueous organic redox flow batteries: a critical review. Chem Rev 2020;120:6467-89.
52. Liu Y, Mu D, Dai Y, Ma Q, Zheng R, Dai C. Analysis on extraction behaviour of lithium-ion battery electrolyte solvents in supercritical CO by gas chromatography. Int J Electrochem Sci 2016;11:7594-604.
53. Amereller M, Schedlbauer T, Moosbauer D, et al. Electrolytes for lithium and lithium ion batteries: from synthesis of novel lithium borates and ionic liquids to development of novel measurement methods. Prog Solid State Ch 2014;42:39-56.
54. Mao Z, Song Y, Zhen AG, Sun W. Recycling of electrolyte from spent lithium-ion batteries. Next Sustain 2024;3:100015.
55. Tao R, Xing P, Li H, Sun Z, Wu Y. Recovery of spent LiCoO2 lithium-ion battery via environmentally friendly pyrolysis and hydrometallurgical leaching. Resour Conserv Recy 2022;176:105921.
56. Lei S, Sun W, Yang Y. Solvent extraction for recycling of spent lithium-ion batteries. J Hazard Mater 2022;424:127654.
57. Zhu Y, Ding Q, Zhao Y, Ai J, Li Y, Cao YC. Study on the process of harmless treatment of residual electrolyte in battery disassembly. Waste Manag Res 2020;38:1295-300.
58. Shi G, Wang J, Zhang S, et al. Green regeneration and high-value utilization technology of the electrolyte from spent lithium-ion batteries. Sep Purif Technol 2024;335:126144.
59. Beolchini F, Fonti V, Dell’Anno A, Rocchetti L, Vegliò F. Assessment of biotechnological strategies for the valorization of metal bearing wastes. Waste Manag 2012;32:949-56.
60. Li J, Zhao R, He X, Liu H. Preparation of LiCoO2 cathode materials from spent lithium–ion batteries. Ionics 2009;15:111-3.
61. Zhao YJ, Sun YC, Ji CW, et al. A kind of waste and old lithium ionic cell electrolyte recovery and treatment method. Available from: https://patents.google.com/patent/CN103825065B/en. [Last accessed on 24 Sep 2024].
62. Zheng X, Zhu Z, Lin X, et al. A mini-review on metal recycling from spent lithium ion batteries. Engineering 2018;4:361-70.
63. Wang K, Li J, Mcdonald R, Browner R. Iron, aluminium and chromium co-removal from atmospheric nickel laterite leach solutions. Miner Eng 2018;116:35-45.
64. Li X, Zhang J, Song D, Song J, Zhang L. Direct regeneration of recycled cathode material mixture from scrapped LiFePO4 batteries. J Power Sources 2017;345:78-84.
65. Xu X, Hong T, Ma H, Yang J. Removal of fluoride from the mixed Ni-Co-Mn sulfate leach solution of spent lithium ion batteries using polyaluminum sulfate. Hydrometallurgy 2023;222:106171.
66. Xiao X, Hoogendoorn BW, Ma Y, et al. Ultrasound-assisted extraction of metals from lithium-ion batteries using natural organic acids. Green Chem 2021;23:8519-32.
67. Esmaeili M, Rastegar SO, Beigzadeh R, Gu T. Ultrasound-assisted leaching of spent lithium ion batteries by natural organic acids and H2O2. Chemosphere 2020;254:126670.
68. He L, Shi L, Huang Q, et al. Extraction of alumina from aluminum dross by a non-hazardous alkaline sintering process: dissolution kinetics of alumina and silica from calcined materials. Sci Total Environ 2021;777:146123.
69. Álvarez E, Romar A, Fernández-Marcos ML. Fluorine immission to acid soil in the vicinity of an aluminium smelter in Galicia (NW Spain) and its influence on aluminium dynamics. J Soils Sediments 2013;13:72-81.
70. Rathi BS, Kumar PS, Rangasamy G, Badawi M, Aminabhavi TM. Membrane-based removal of fluoride from groundwater. Chem Eng J 2024;488:150880.
71. Chae Y, Kim D, An YJ. Effects of fluorine on crops, soil exoenzyme activities, and earthworms in terrestrial ecosystems. Ecotoxicol Environ Saf 2018;151:21-7.
72. Kessabi M, Assimi B, Braun JP. The effects of fluoride on animals and plants in the south Safi zone. Sci Total Environ 1984;38:63-8.
74. Giri A, Bharti VK, Angmo K, Kalia S, Kumar B. Fluoride induced oxidative stress, immune system and apoptosis in animals: a review. IJB 2016;5:5174.
75. Nizam S, Virk HS, Sen IS. High levels of fluoride in groundwater from Northern parts of Indo-Gangetic plains reveals detrimental fluorosis health risks. Environ Adv 2022;8:100200.
76. Dehghani MH, Zarei A, Yousefi M, Asghari FB, Haghighat GA. Fluoride contamination in groundwater resources in the southern Iran and its related human health risks. Desalin Water Treat 2019;153:95-104.
77. Sahu BL, Banjare GR, Ramteke S, Patel KS, Matini L. Fluoride contamination of groundwater and toxicities in Dongargaon Block, Chhattisgarh, India. Expo Health 2017;9:143-56.
78. Yousefi M, Ghalehaskar S, Asghari FB, et al. Distribution of fluoride contamination in drinking water resources and health risk assessment using geographic information system, northwest Iran. Regul Toxicol Pharmacol 2019;107:104408.
79. Yousefi M, Ghoochani M, Hossein Mahvi A. Health risk assessment to fluoride in drinking water of rural residents living in the Poldasht city, Northwest of Iran. Ecotoxicol Environ Saf 2018;148:426-30.
80. Mohammadi AA, Yousefi M, Yaseri M, Jalilzadeh M, Mahvi AH. Skeletal fluorosis in relation to drinking water in rural areas of West Azerbaijan, Iran. Sci Rep 2017;7:17300.
81. Yousefi M, Yaseri M, Nabizadeh R, et al. Association of hypertension, body mass index, and waist circumference with fluoride intake; water drinking in residents of fluoride endemic areas, Iran. Biol Trace Elem Res 2018;185:282-8.
82. Cao J, Chen Y, Chen J, Yan H, Li M, Wang J. Fluoride exposure changed the structure and the expressions of Y chromosome related genes in testes of mice. Chemosphere 2016;161:292-9.
83. Alexander BH, Olsen GW. Bladder cancer in perfluorooctanesulfonyl fluoride manufacturing workers. Ann Epidemiol 2007;17:471-8.
84. Yang CY, Cheng MF, Tsai SS, Hung CF. Fluoride in drinking water and cancer mortality in Taiwan. Environ Res 2000;82:189-93.
85. Ge D, Huang S, Cheng J, et al. A new environment-friendly polyferric sulfate-catalyzed ozonation process for sludge conditioning to achieve deep dewatering and simultaneous detoxification. J Clean Prod 2022;359:132049.
86. Yin C, Yu S, An B, et al. Fluorine recovery from etching wastewater through CaF2-based near-infrared photocatalyst synthesis. J Clean Prod 2018;175:267-75.
87. Dobó Z, Dinh T, Kulcsár T. A review on recycling of spent lithium-ion batteries. Energy Rep 2023;9:6362-95.
88. Zhou LF, Yang D, Du T, Gong H, Luo WB. The current process for the recycling of spent lithium ion batteries. Front Chem 2020;8:578044.
89. Yang K, Gong P, Tian Z, Lai Y, Li J. Recycling spent carbon cathode by a roasting method and its application in Li-ion batteries anodes. J Clean Prod 2020;261:121090.
90. Zhu Z, Xu L, Han Z, et al. Optimization of response surface methodology (RSM) for defluorination of spent carbon cathode (SCC) in fire-roasting aluminum electrolysis. Miner Eng 2022;182:107565.
91. Fujii T, Kashimura K, Tanaka H. Microwave sintering of fly ash containing unburnt carbon and sodium chloride. J Hazard Mater 2019;369:318-23.
92. Liu X, Bouxin FP, Fan J, Budarin VL, Hu C, Clark JH. Microwave-assisted catalytic depolymerization of lignin from birch sawdust to produce phenolic monomers utilizing a hydrogen-free strategy. J Hazard Mater 2021;402:123490.
93. Zhu Z, Xu L, Han Z, et al. Defluorination study of spent carbon cathode by microwave high-temperature roasting. J Environ Manage 2022;302:114028.
94. Dong L, Jiao F, Liu W, Wang C, Wang D, Qin W. A novel approach for extracting lithium from overhaul slag by low temperature roasting - water leaching. Chem Eng J 2024;481:148571.
95. Su F, Zhou X, Liu X, et al. Efficient recovery of valuable metals from spent Lithium-ion batteries by pyrite method with hydrometallurgy process. Chem Eng J 2023;455:140914.
96. Xi F, Li S, Ma W, Chen Z, Wei K, Wu J. A review of hydrometallurgy techniques for the removal of impurities from metallurgical-grade silicon. Hydrometallurgy 2021;201:105553.
97. Lisbona D, Steel K. Recovery of fluoride values from spent pot-lining: precipitation of an aluminium hydroxyfluoride hydrate product. Sep Purif Technol 2008;61:182-92.
98. Lisbona DF, Somerfield C, Steel KM. Leaching of spent pot-lining with aluminium nitrate and nitric acid: effect of reaction conditions and thermodynamic modelling of solution speciation. Hydrometallurgy 2013;134-5:132-43.
99. Wu S, Tao W, Han W, et al. Hydrometallurgical stepwise separation of alumina and recovery of aluminum fluoride from waste anode cover material of aluminum electrolysis. Miner Eng 2022;186:107740.
100. Nie Y, Guo X, Guo Z, Tang J, Xiao X, Xin L. Defluorination of spent pot lining from aluminum electrolysis using acidic iron-containing solution. Hydrometallurgy 2020;194:105319.
101. Tao W, Yang J, Chen L, et al. Environmentally friendly and efficient green recovery of fluoride from waste aluminum electrolytic sediment using Al2O3. Sep Purif Technol 2023;317:123934.
102. Yao Z, Zhong Q, Xiao J, Ye S, Tang L, Zhang Z. An environmental-friendly process for dissociating toxic substances and recovering valuable components from spent carbon cathode. J Hazard Mater 2021;404:124120.
103. Yao Z, Xiao J, Mao Q, et al. Detoxification and recovery of spent carbon cathodes via NaOH–Na2CO3 binary molten salt roasting - water leaching: toward a circular economy for hazardous solid waste from aluminum electrolysis. ACS Sustainable Chem Eng 2020;8:16912-23.
104. Li H, Huang Y, Yang X, Jiang Z, Yang Z. Approach to the management of magnesium slag via the production of Portland cement clinker. J Mater Cycles Waste Manag 2018;20:1701-9.
105. Gao X, Yao X, Yang T, Zhou S, Wei H, Zhang Z. Calcium carbide residue as auxiliary activator for one-part sodium carbonate-activated slag cements: compressive strength, phase assemblage and environmental benefits. Constr Build Mater 2021;308:125015.
106. Xie G, Suo Y, Liu L, et al. Mechanical grinding activation of modified magnesium slag and its use as backfilling cementitious material. Case Stud Constr Mat 2023;18:e01778.
107. Ji G, Peng X, Wang S, et al. Influence of magnesium slag as a mineral admixture on the performance of concrete. Constr Build Mater 2021;295:123619.
108. Zhu P, Chen Y, Wang LY, et al. Preparation of anorthite ceramic using mining tailings and calcium fluoride sludge. Can Metall Quart 2013;52:190-8.
109. Zhu P, Cao Z, Ye Y, et al. Reuse of hazardous calcium fluoride sludge from the integrated circuit industry. Waste Manag Res 2013;31:1154-9.
Cite This Article

How to Cite
Zhao, H.; Zhang X.; Pan D. Research progress on comprehensive utilization of fluorine-containing solid waste in the lithium battery industry. Green. Manuf. Open. 2024, 2, 15. http://dx.doi.org/10.20517/gmo.2024.070201
Download Citation
Export Citation File:
Type of Import
Tips on Downloading Citation
Citation Manager File Format
Type of Import
Direct Import: When the Direct Import option is selected (the default state), a dialogue box will give you the option to Save or Open the downloaded citation data. Choosing Open will either launch your citation manager or give you a choice of applications with which to use the metadata. The Save option saves the file locally for later use.
Indirect Import: When the Indirect Import option is selected, the metadata is displayed and may be copied and pasted as needed.
About This Article
Special Issue
Copyright
Data & Comments
Data
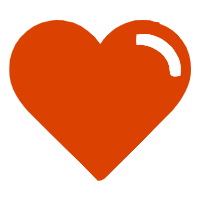
Comments
Comments must be written in English. Spam, offensive content, impersonation, and private information will not be permitted. If any comment is reported and identified as inappropriate content by OAE staff, the comment will be removed without notice. If you have any queries or need any help, please contact us at support@oaepublish.com.