Wind turbine foundation ring fatigue reliability analysis under wind-load using SCADA system
Abstract
Under the action of wind load, the foundation ring of the fan will generate stress concentration and alternating stress, leading to fatigue failure. Based on the average wind speed obtained from the supervisory control and data acquisition (SCADA) system, the orthogonal expansion method of random pulsating wind field and the number theory point selection method are used to calculate and simulate the corresponding pulsating wind speed time series, and then calculate the wind speed time series and wind load time series. Based on the ABAQUS finite element software, a model of a 5 MW wind turbine is established. The modal analysis is used to obtain the modal vibration pattern and the intrinsic frequency to verify the reasonableness of the structural modeling. Subsequently, the wind load time series is applied to the wind turbine model to obtain the stress time series using instantaneous modal dynamic analysis (Modal dynamics). The stress time series at the location of maximum stress concentration in the foundation ring is extracted, and the stress time series with the same stress amplitude is obtained through conversion, which has Wiener characteristics. After obtaining the stress amplitude using the rainflow counting method, the fatigue reliability is calculated based on the structural fatigue reliability analysis method considering the threshold crossing duration of the random process. This research holds reference significance for the calculation of fatigue reliability under approximate working conditions.
Keywords
INTRODUCTION
Most collapse accidents of wind turbine structures are caused by fatigue damage to the concrete foundation or connecting bolts of the wind turbine under wind load, leading to noticeable sliding displacement and structural collapse. Currently, although a large amount of analysis has been conducted on the reliability of wind turbine structures, the various uncertainties present in the natural environment and the operation process make it difficult to accurately assess the fatigue reliability of wind turbine structures using constant reliability statistical indicators. Therefore, research on the fatigue reliability of wind turbines is relatively limited. Therefore, it is of great practical significance and economic value to use real-time monitoring data from supervisory control and data acquisition (SCADA) systems to establish a structural model of wind turbines and conduct fatigue reliability analysis. Condition monitoring is an important means to improve the operational safety of wind turbines and is of great significance for the safe and efficient utilization of the turbine structure[1-9]. Monitoring techniques for wind turbine structures mainly include ultrasonic testing, thermal imaging, process parameter monitoring, performance parameter monitoring, and X-ray imaging techniques. Currently, the most widely used real-time monitoring system for wind turbine structures is the SCADA system, which can monitor the operation status of all components or subsystems of the turbine structure in real-time. It integrates information collection, condition monitoring, and parameter adjustment, providing technical support for the long-term safe operation of wind turbine structures.
The SCADA system of wind turbines has the capability of real-time monitoring and data acquisition, and many scholars have utilized this system to solve problems that are more in line with actual operating conditions. Kusiak et al. used historical operating data of wind turbine structures to select relief algorithm characteristic parameters for the “three-blade asymmetry” and “abnormal pitch angle” faults of the variable pitch system[10]. Gill et al. used SCADA system operating data to establish a probability model of the power curve of the wind turbine structure based on Copula functions, effectively monitoring early signs of blade degradation, yawing, and variable pitch system faults[11]. Kusiak et al. used the Hotelling’s T2 statistical method to analyze the active power operating data of the turbine, identifying the operating state of the entire unit[12]. Zaher et al. developed an automatic anomaly detection system that identifies early turbine faults through automatic analysis of online SCADA data[13]. Garcia et al. used SCADA operating data to establish a gearbox temperature model, evaluating the health condition of the gearbox by continuously monitoring the prediction confidence interval of the model[14]. Yang et al. proposed the use of SCADA data monitoring technology to assess the health status of different operating conditions, detect early faults in blades and drive systems, and track their further deterioration[15]. Zhang et al. proposed a dynamic model sensor approach for wind turbine fault detection based on SCADA data, as the changes in measurement capabilities of the hardware sensors used in current SCADA systems often fail to provide reliable early warnings[16]. Zhang et al. proposed health condition evaluation indicators for wind turbine units based on the relationship with SCADA (monitoring and data acquisition) data[17]. Tang et al. developed a novel fault diagnosis and prediction method based on support vector regression models using data obtained from the monitoring and data acquisition system (SCADA) of wind turbines[18]. Liu developed a new state monitoring and fault isolation system to address inherent issues in SCADA data analysis, including low sampling rates, time-varying operating conditions of wind turbine units, and a lack of historical fault data[19].
In recent years, there have been frequent incidents of wind turbine foundation ring detachment from the surrounding concrete or damage to the connection between the foundation and the upper tower structure. These incidents have resulted in excessive tower oscillation, turbine alarms, shutdowns, and even collapses, causing significant economic losses that are difficult to estimate. The main cause of these problems is excessive fatigue loads. Therefore, the fatigue reliability analysis of wind turbine structures has attracted widespread attention from researchers. For example, Velarde et al. proposed a reliability-based framework for calibrating the partial safety factors of fatigue in offshore wind turbine concrete structures[20]. They used a fully integrated aeroelastic model to estimate the load on offshore wind turbines considering the statistical distribution of turbulence intensity. Based on existing fatigue tests, they established a fatigue reliability model for concrete and applied it to two numerical examples. The results showed that the recommended partial safety factors for materials in the Det Norske Veritas (DNV) standard can be reduced for offshore concrete structures without compromising structural safety. Wang et al. studied the fatigue damage of offshore wind turbine foundations using stress accumulation methods and found that the coupling effect of wind and wave loads has a significant impact on the overall fatigue damage of wind turbine structures[21].
This article focuses on the fatigue reliability of the foundation ring of wind turbines. The reliability analysis of the structure under long-term wind loads belongs to the field of structural dynamic reliability analysis, which involves two failure mechanisms: exceedance failure mechanism[28-30] and fatigue failure mechanism[31,32]. Structural fatigue failure is caused by the accumulation of damage due to the structure exceeding the safety threshold multiple times during the response process. Therefore, the probability analysis of multiple threshold crossings in stochastic processes should be considered in fatigue reliability assessment.
Based on recent advancements in the analysis of stochastic processes and multiple threshold crossings[33,34], as well as the availability of real-time monitoring data through SCADA systems to determine average wind speeds, this study employs the orthogonal expansion method[22] and the number theory method[35] to simulate the pulsating wind speed-time series. By generating the stochastic wind speed-time series, the wind load acting on the wind turbine can be calculated. The wind turbine structure is modeled using ABAQUS finite element software, and the obtained wind load-time series is applied to the model to obtain the stress-time series at the stress concentration of the wind turbine foundation ring. Considering the significant impact of the duration of the stochastic response process beyond the damage threshold (referred to as crossing-threshold duration) on the fatigue reliability of the wind turbine structure, it is important to use a structural fatigue reliability analysis method that considers the stochastic process of crossing-threshold holding time. This approach is more representative of the actual fatigue reliability analysis of the wind turbine foundation ring, and it has practical implications for engineering applications.
CALCULATIONS OF WIND SPEED-TIME SERIES AND WIND LOAD-TIME SERIES
Overview of the wind turbine engineering
ABAQUS is utilized to conduct finite element modeling and analysis of a 5 MW wind turbine generator. The main parameters of the wind turbine are as follows. The height of the generator rotor is 80 m, the diameter of the rotor is 115 m, the rated wind speed is 11.9 m/s, and the design life is 20 years. The nacelle of the turbine weighs 131.142 t. The rotor consists of three blades and a hub, with each blade’ length being 55 m. The total weight of the rotor is 68.283 t, and the rated rotational speed is 14.3 rpm. The wind turbine tower is composed of three sections of variable cross-section steel tower, with geometric parameters shown in Table 1. The wind turbine foundation adopts a circular pedestal-type expanded foundation, with a ground diameter of 18.8 m and a burial depth of 3.4 m. The tower and foundation ring are made of Q345 steel, and the foundation concrete is made of C40 concrete.
The geometric parameters of each tower of the wind turbine
Tower | Height (m) | Bottom outer diameter (m) | Top outer diameter (m) | wall thickness (m) |
Lower section | 14.86 | 4.5 | 4.5 | 0.05 |
middle section | 28.315 | 4.5 | 3.9 | 0.05 |
upper section | 32.102 | 3.9 | 3.07 | 0.02 |
Calculation of wind speed-time series
In order to obtain real-time operational condition factors of wind turbines, most wind farms are equipped with SCADA systems, which can monitor and collect data in real time, with a data collection interval of seconds. There are limitations in obtaining data through SCADA systems, such as incomplete and inaccurate data, etc. In order to alleviate these problems, the data used in this paper is the average wind speed ν80 = 16.74 m/s at the rotor of the wind turbine collected by the SCADA system during normal operation within a day.
The wind speed time series at a certain height z is equal to the average wind speed plus the fluctuating wind speed time series. The average wind speed at each height is obtained using wind speed conversion formulas. The random fluctuating wind field is calculated and simulated using the orthogonal expansion method[22] and number theory point selection method[35], and the wind speed time series at a certain height z is obtained accordingly. The wind speed time series is calculated by
where
In order to simplify the calculation, the tower of a 75 m high wind turbine tower is divided into 0~15, 15~45 and 45~75 m, and the wind speed at the center of the three sections is taken as the average wind speed of the tower in the section, i.e., the average wind speed at 7.5, 30 and 60 m. The conversion for the average wind speed at each height is expressed as follows.
where λ is the ground roughness coefficient; k is the conversion coefficient of different landforms. According to the “Standard for design of high-rising structure”[36], it can be seen that the wind farm is located in the landform of class B; the value of λ is 0.16, and the value of k is 1.0.
In the case where the power spectral density (PSD) function of the pulsating wind speed-time series
where U(θ;z) is a random field that responds to the spatial correlation of pulsating wind speeds; ν(t) is a stochastic process that responds to the pulsating wind properties.
According to the Literature[22], it can be obtained that the stochastic process ν(t) that responds to the pulsating wind characteristics can be represented by an orthogonal expansion as
where N is the number of unfolding terms taking the value of 600; r is the truncation coefficient taking the value of 10 (The first 10 eigenvalues account for about 90% of the total energy, and the random variables of their corresponding eigenvalues can reflect the main probabilistic properties of the virtual pulsating wind displacement process[22]); χn+1(n = 1, 2…, N) is a set of harmonic energy adjustment coefficients, which is mainly introduced to consider the error caused by truncation; λj is the j-th eigenvalue of the correlation matrix R of the stochastic process of pulsating wind speed based on the Fourier mean spectrum; φj,n+1 is the
For the correlation matrix R = [ρij]N×N, the autocorrelation function ρij (only related to the time interval
where the deterministic function ϕk(t) is the Hartley orthogonal basis function, where cas(t) = cos(t) + sin(t); T is the length of time which takes the value of 600 s.
Construct the corresponding autocorrelation function of the virtual pulsating wind displacement random process u(t) based on the equivalent pulsating wind characteristic random process ν(t), as given in[22]
where
Because the wind speed at the center point of each tower section and at the impeller is mainly considered, for Eq. (3), there is[22]
where {ξj(θ), j = 1, 2, 3…rz} is consistent with Eq. (4), and it is also a set of mutually independent standard Gaussian random vectors; for the building within 150 m in this paper, rz = 5[22] can meet the required accuracy;
The reaction pulsating wind characteristic stochastic process ν(t) and the reaction pulsating wind speed spatial correlation random field U(θ;z) where the dimensionless set of random variables {ξj, j = 1, 2, 3…r} and {ξj(θ), j = 1, 2, 3…rz} satisfy[22]
where δij is the Kronecker-delta symbol.
If the stochastic process of pulsating wind speed and its virtual wind displacement can be assumed to be the Gaussian process, then the sets of random variables {ξj, j = 1, 2, 3…r} and {ξj(θ), j = 1, 2, 3…rz} are both mutually independent sets of standard Gaussian random variables. Utilizing the number theory point selection method[35], a data table that provides vectors according to Literature[37] can be used to select points directly. In this paper, the MATLAB program is used to implement the number theory point selection method, and the number of selections in the hypersphere is Nsel = 180; i.e., 180 standard Gaussian random variable sets are obtained from the screening. Based on 180 standard Gaussian random variable groups, MATLAB software is used to write programs. Since the SCADA system collects data at one-second intervals, and wind speeds are converted to reflect the 10 m height standard in our country, we used the
Calculation of wind load-time series
The standard value of wind loads perpendicular to the surface of the wind turbine tower according to “Standard for design of high-rising structure”[36] is calculated according to
where Fki is the wind load standard value of each section of the wind turbine tower; ωk is the standard value of wind load acting on the unit projection area at the height z of the wind turbine tower; ω0 is the basic wind pressure, which takes the value of 0.55 kN/m2 according to the site conditions where the wind turbine is located; hi is the height of each section of the wind turbine tower; di is the diameter of the center point of each section of the wind turbine tower; βz is the wind vibration coefficient at height z; μz is the wind pressure height change coefficient at height z of the wind turbine tower; μs is the wind load body type coefficient, taking the value of 0.7. βz and μz are obtained by taking values according to the specification[36].
Given the wind speed time series acting on the tower body, the corresponding wind load acting on the wind turbine tower body is calculated according to
where Fi is the wind load corresponding to each section of the wind turbine tower; ωp is the wind pressure at the corresponding height z.
According to the Bernoulli's theory the relationship between wind speed and wind pressure can be obtained as
where ρ is the air density; Vt is the wind speed-time course at the impeller under normal operating conditions of the wind turbine.
For the wind load on the tower blades, it can be divided into two specific cases: normal operating conditions and extreme load conditions. Due to the obtained data in this paper being wind speeds obtained during normal operation of the wind turbine, the effects of extreme loads are not considered for now. Under normal operating conditions, the thrust force of the blade due to the wind load can be calculated according to the following equation, based on the momentum-blade element theory.
where A is the wind turbine blade swept area; CT is the thrust coefficient. The thrust coefficients of the wind turbine are different at different wind speeds and the thrust coefficients of this 5 MW wind turbine are given by the manufacturer as shown in Figure 5.
The wind speed-time series of the wind turbine tower at 0~15, 15~45, 45~75 m is brought into Eq. (15) respectively, and the total wind load-time series acting on each section of the tower can be calculated out, as given in Figures 6-8.
The wind speed-time series at the impeller of the wind turbine under normal operating conditions is brought into Eq. (17) to obtain its corresponding total wind load-time series, as shown in Figure 9.
NUMERICAL SIMULATION OF WIND TURBINE STRUCTURE USING ABAQUS
Establishment of wind turbine model in ABAQUS
The focus of this study is on the foundation ring, so the model has been simplified for ease of modeling, mainly divided into three major parts: (1) upper structure; (2) tower body; and (3) foundation. The upper structure consists of the hub, blades, and nacelle, while the foundation includes the concrete foundation and the foundation ring. The tower body is modeled based on the actual geometric parameters in Table 1. Considering that the vibration characteristics of the wind turbine structure mainly depend on the tower body, the modeling of the upper structure is simplified. In order to ensure that the overall stiffness and mass remain unchanged, an equivalent modeling approach is adopted. The material properties used in the equivalent modeling have a density of 258.26 kg·m-3, an elastic modulus of 200 GPa, and a Poisson’s ratio of 0.3. The material properties for the remaining parts are set according to their actual properties, as shown in Tables 2 and 3.
Material properties
Name of material | Density (kg·m-3) | Modulus of elasticity (GPa) | The Poisson's ratio | Standard value of tensile strength (MPa) | Standard value of compressive strength (MPa) |
C40 Concrete | 2500 | 32.5 | 0.2 | 2.39 | 26.8 |
Q345 Steel | 7850 | 200 | 0.3 | 345 | 345 |
Steel Q345 hardening curve
Stress σ (MPa) | 414 | 465 | 543 | 606 | 671 | 708 | 773 |
Strain ε (%) | 0 | 0.0428 | 0.903 | 0.1384 | 0.1782 | 0.2175 | 0.2663 |
Since the focus of this study is on the fatigue reliability and fatigue life of the foundation ring, the modeling of the steel reinforcement in the concrete foundation and the modeling below the foundation are abandoned. Tie connections are used between the hub and nacelle, nacelle and tower body, and tower body and foundation ring. The concrete foundation and the foundation ring are in face-to-face contact, with Coulomb friction contact in the tangential direction and a friction coefficient of 0.35. The normal contact is treated as hard contact. Regarding the boundary conditions, the concrete foundation ground is assumed to have a fully fixed boundary condition since the modeling of the foundation is not considered. The mesh division for each component is as follows: the blades and hub use solid elements C3D10, the nacelle, concrete foundation, and tower body use solid elements C3D8R, and the foundation ring uses shell elements S4R. The overall mesh division is shown in Figure 10, and the mesh division for the focus on the foundation ring is shown in Figure 11.
Since the wind speed collected in real time by the SCADA system in this study is the wind speed on the windward side, the wind load is only applied to the windward side of the turbine rotor and tower body. The total wind load received at heights of 0-15, 15-45, 45-75 m, and at the rotor is established as “amplitude” based on the corresponding relationship between time and load values. In the ABAQUS finite element software, the 75 m high tower body is divided into three sections, and reference points RP-1 to RP-3 are established at the center of each section. Each reference point is coupled with the corresponding surface of the tower body, and the loads acting on each section of the tower body are applied to the reference points. As for the total wind load-time series acting on the turbine rotor, since the main focus of the study is on the foundation ring, a concentrated load method is used to apply the load to the center of the rotor hub.
The modal analysis of the wind turbine structural model in ABAQUS
Based on the ABAQUS model established in Section "Establishment of wind turbine model in ABAQUS", in order to ensure that the wind turbine does not collapse due to resonance between low-order natural frequencies and rotor rotation frequencies (The difference between the higher order intrinsic frequency of the wind turbine and the rotational frequency of the impeller is large, and due to the role of structural damping, the higher order part of the dynamic response attenuates very quickly), modal analysis is conducted before performing transient modal dynamic analysis in ABAQUS finite element software. Therefore, the wind turbine model is first subjected to modal analysis to obtain its low-order natural frequencies.
Modal analysis is performed in ABAQUS, without considering the influence of loads, only setting boundary conditions. This study only aims to obtain the first four natural frequencies of the wind turbine, so the subspace iteration method is used for faster calculation results. The calculated natural frequencies of the wind turbine are shown in Table 4, and the modal shapes are shown in Figure 12. From the figure, it can be observed that the low-order modal shapes of the wind turbine mainly exhibit bending and swinging forms.
Figure 12. Wind turbine first 4th order mode shapes; (A) First-order mode shapes; (B) Second-order mode shapes; (C) Third-order mode shapes; (D) Fourth-order mode shapes.
Wind turbine first 4th order natural frequency
Ordinal number | 1 | 2 | 3 | 4 |
Natural frequency (Hz) | 0.37680 | 0.37759 | 0.6420 | 0.80267 |
The rated speed of the 5 MW wind turbine rotor is known to be 14.3 r/min. From calculations, the rotational frequency of the rotor can be determined as f = 14.3/60 Hz = 0.2383 Hz. The rotor has three blades, and it is known from literature[38] that the prerequisite for avoiding resonance between the wind turbine tower and the rotor is that the relative difference between the natural frequency of the tower and the rotor rotation frequency or three times the rotor rotation frequency (3f = 0.7149 Hz, i.e., the passing frequency of the blades) should be greater than 10%. The relative differences between the calculated natural frequencies in Table 3 and the rotor rotation frequency are shown in Table 5, and all the relative differences are greater than 10%. Therefore, there will be no resonance between the wind turbine tower and the rotor, thus verifying the correctness of the wind turbine structure model established in this paper.
Relative difference between the first 4 orders of the wind turbine
Ordinal number | 1 | 2 | 3 | 4 |
Relative difference with f (%) | 58.12 | 58.45 | 169.41 | 236.83 |
Relative difference with 3f (%) | -47.29 | -47.18 | -10.20 | 12.28 |
Transient modal dynamics analysis of the wind turbine model in ABAQUS
In the transient modal dynamic analysis, Rayleigh damping is considered. According to Table 3, the damping coefficients α and β corresponding to the first and second natural frequencies of the wind turbine are calculated by
where ξ is the structural vibration damping ratio, which is taken as 0.05 according to the “Standard for design of high-rising structure”[36]; ω1 and ω2 are the circular frequencies of the 1st and 2nd vibration modes, respectively, and ωi = 2πfi, fi is the i-th order intrinsic frequencies of the wind turbine.
By substituting the first and second natural frequencies of the wind turbine from Table 3 into Eqs. (18) and (19), the calculated Rayleigh damping coefficients α = 0.11850 and β = 0.02110 can be obtained.
The wind load calculated in Section "Calculation of wind load-time series" is applied to the wind turbine model. Then, the Rayleigh damping coefficients α and β are input into the modal dynamics analysis step of the ABAQUS finite element software to perform transient modal dynamic response analysis, thereby obtaining the stress-time series. The stress contour map of the foundation ring, which is the main focus of the study, is shown in Figure 13. By observing the figure, it can be seen that the red region in the figure, which corresponds to the flange edge of the foundation ring, is the area with the highest stress. This is consistent with the occurrence of the highest stress area in the structure in actual engineering. The stress-time series of this maximum stress region is extracted and shown in Figure 14.
Discussion for applicability of FE model
The model used above is a 5 MW wind turbine. Because of its high power generation rate, it is more commonly used in the field of wind power generation, especially in some areas rich in wind resources (including the seaside). The dimensions and material properties of the wind turbine are obtained from the manufacturer. In performing the ABAQUS finite element modeling and analysis, the structure is modeled in a simplified manner, such as the superstructure is modeled in an equivalent manner for ease of computation and generalizability, which can be used for the study of this type of 5 MW wind turbine. This paper focuses on the fatigue reliability at the maximum stress at the edge of the flange on the base ring of a wind turbine. The fatigue reliability of the flange edge on the base ring is analyzed by the fatigue reliability calculation method considering the crossing-threshold duration, and a comparative analysis is made by the traditional method. The method is generalized and can be used for other types and sizes of wind turbine structures, and is also applicable to the calculation of stress-fatigue reliability of structures in different environments.
FATIGUE RELIABILITY ANALYSIS OF FOUNDATION RING CONSIDERING CROSSING-THRESHOLD DURATION OF RANDOM PROCESS
Stress-time histories characterized by Wiener processes
According to the “Standard for design of steel structures”[39], the stress amplitude of lower than the fatigue cut-off limit [ΔσL], that is, Δσ = σmax - σmin < [ΔσL], will not lead to fatigue damage. Therefore, it can be concluded that fatigue damage is mainly related to the stress amplitude, and not directly related to the maximum and minimum stress values. Therefore, the stress-time series of the maximum stress region of the foundation ring is obtained by subtracting its mean value, as shown in Figure 15. At the same time, the effect of tensile-averaged stress on fatigue damage cannot be neglected because the stress average
Figure 15. Stress-time series in the stress-concentration region of the modified wind turbine foundation ring.
The stress-time series of a structure under load can be considered as a stochastic process. And some stress-time histories of structures can be approximated as Wiener processes, which have the characteristics of a Wiener process. Figure 16 shows a sample curve of a Wiener process (with a duration of 1,200 and 200 s). By comparing it with the stress-time series of the new maximum stress region of the foundation ring in Figure 15, it is found that the long-term Wiener process (e.g., 1,200 s) does not match the stress-time series, but the short-term Wiener process (e.g., 200 s) is more similar to the stress-time series. At the same time, the stress variation process of the maximum stress region of the foundation ring in normal operation of the wind turbine shows similarity; i.e., the entire random stress spectrum can be regarded as a repetition of typical stress-time load spectra. Therefore, it is assumed that the short-term Wiener process can be regarded as a typical stress-time spectrum block, and based on the similarity between the short-term Wiener process and the stress-time series, the stress-time series of the maximum stress region of the foundation ring can be considered as a repetition of stress-time histories based on short-term Wiener processes.
Structural fatigue reliability analysis
Based on the progress of the analysis of multiple threshold crossings of stochastic processes in recent years[33], the structural fatigue reliability analysis method considering the crossing-threshold duration of stochastic processes is used to analyze the fatigue reliability of structures. The calculation formula is as follows[40].
where x1 refers to the number of threshold crossings for the cyclic process of stresses within a periodic short time period tshort; in this paper, tshort =100 s; i is the number of periodic short time periods tshort within the normal running time length T, i.e., i = T/tshort; Ne is that the statistically obtained number of stress cycles per day is about 5.00 × 106 times; E(Sm) is the m-order moment of origin of the stress amplitude S; m and C are the correlation coefficients of components and connections, according to the “Standard for design of steel structures”[39], the components and connection types are selected as Z8, take m = 3, C = 0.72 × 1012; q is the length of time taken for the stress to cycle once; b is the damage threshold, according to the “Standard for design of steel structures”[39], when the stress amplitude is lower than the fatigue cut-off limit will not lead to fatigue damage, so take the stress amplitude at times N = 1 × 108 as the fatigue cut-off limit, i.e., b =
The connection between the foundation ring and the tower is made using a flange connection. The maximum stress generated at the upper flange of the foundation ring can significantly reduce the fatigue strength at the upper flange and bolt locations. The research object is selected as the location of the maximum stress at the upper flange of the foundation ring, and its stress-time series is shown in Figure 17. It is now corrected for equivalent stresses, and the material strength is taken as 345 MPa. Subsequently, the rainfall counting method is applied to this data to obtain its 16-level stress spectrum, as shown in Table 6.
Statistics of stress amplitude
Amplitude/MPa | 19.70 | 21.05 | 22.40 | 23.74 | 25.09 | 26.44 | 27.79 | 29.14 |
Times (×103) | 103.45 | 321.84 | 804.60 | 1,011.49 | 965.52 | 413.79 | 114.94 | 183.91 |
Frequency | 0.02069 | 0.06437 | 0.16092 | 0.2023 | 0.1931 | 0.08276 | 0.02299 | 0.03678 |
Amplitude/MPa | 30.48 | 31.83 | 33.18 | 34.53 | 35.87 | 37.22 | 38.57 | 39.92 |
Times (×103) | 149.43 | 333.33 | 160.92 | 195.40 | 149.43 | 34.48 | 22.99 | 34.48 |
Frequency | 0.02989 | 0.06667 | 0.03218 | 0.03908 | 0.02989 | 0.0069 | 0.0046 | 0.0069 |
According to the data in Table 6 and the member and connection correlation coefficient m = 3, it is possible to obtain:
x1 is the number of times the stress cycling process crosses the damage threshold b in a periodic short time period tshort, which needs to be generated by simulation with the MATLAB program. Through tshort = 100 s, it can be obtained that in 100 s, in order to accurately require to take dt = 0.01 s, through the MATLAB program simulation to generate 10,000 standard Wiener process curves. The value of the number of crossings x1 of this sample curve with the damage threshold b was counted, as shown in Table 7.
Statistics on the number of threshold crossings (tshort = 100 s, b = 29)
Value range of crossing times | The number of samples | Frequency |
[0, 50] | 6,472 | 64.72% |
(50, 100] | 2,351 | 23.51% |
(100, 150] | 890 | 8.9% |
(150, 200] | 234 | 2.34% |
(200, 250] | 45 | 0.45% |
(250, 300] | 6 | 0.06% |
(300, 350] | 2 | 0.02% |
The next step is to calculate the value on the right side of Eq. (20), i.e., calculating
Values of U (tshort = 100 s, tshort = 200 s, b = 29)
T (Unit: years) | 0 | 1 | 2 | 3 | 4 | 5 | 6 |
U (times) | - | 303 | 151 | 101 | 76 | 61 | 50 |
T (Unit: years) | 7 | 8 | 9 | 10 | 11 | 12 | 13 |
U (times) | 43 | 38 | 34 | 30 | 28 | 25 | 23 |
T (Unit: years) | 14 | 15 | 16 | 17 | 18 | 19 | 20 |
U (times) | 22 | 20 | 19 | 18 | 17 | 16 | 15 |
The probability of statistically obtaining the number of crossings x1 and the value of U in Table 8 are uniformly brought into Eq. (20). The fatigue reliability of the stress concentration area of the flange on the base ring over time can be calculated, as shown in Table 9, Figure 18. Similarly, the case of periodic short time duration of 200 s was also calculated, and its U values are shown in Table 8, and the fatigue reliability is shown in Table 10 and Figure 18.
Figure 18. The fatigue reliability curves for flange stress concentration areas on the base ring (tshort = 100 s and 200 s, b = 29).
The fatigue reliability of flange stress concentration areas on the base ring (tshort = 100 s, b = 29)
T (Unit: years) | 0 | 1 | 2 | 3 | 4 | 5 | 6 |
Reliability (%) | 100 | 99.98 | 97.24 | 88.45 | 79.24 | 71.37 | 64.72 |
T (Unit: years) | 7 | 8 | 9 | 10 | 11 | 12 | 13 |
Reliability (%) | 59.80 | 56.45 | 53.32 | 50.08 | 48.46 | 46.29 | 44.52 |
T (Unit: years) | 14 | 15 | 16 | 17 | 18 | 19 | 20 |
Reliability (%) | 43.79 | 42.05 | 41.22 | 40.27 | 39.39 | 38.46 | 37.59 |
The fatigue reliability of flange stress concentration areas on the base ring (tshort = 200 s, b = 29)
T (Unit: years) | 0 | 1 | 2 | 3 | 4 | 5 | 6 |
Reliability (%) | 100 | 99.62 | 87.98 | 72.75 | 61.98 | 54.80 | 48.83 |
T (Unit: years) | 7 | 8 | 9 | 10 | 11 | 12 | 13 |
Reliability (%) | 44.82 | 41.76 | 39.49 | 36.86 | 35.71 | 33.77 | 32.50 |
T (Unit: years) | 14 | 15 | 16 | 17 | 18 | 19 | 20 |
Reliability (%) | 31.82 | 30.60 | 29.88 | 29.17 | 28.50 | 27.77 | 26.98 |
From Figure 18, it can be observed that the fatigue reliability of the maximum stress region at the upper flange of the foundation ring decreases with time. This means that the probability of fatigue failure at the upper flange of the foundation ring grows with the service time. This also increases the probability of detachment between the foundation ring and the upper connecting structure of the wind turbine tower. Furthermore, this leads to overall instability of the wind turbine structure, resulting in alarm shutdown or collapse. Therefore, during the service life of the wind turbine structure, it is necessary to strengthen monitoring in this area and take timely reinforcement and maintenance measures to avoid accidents and economic losses within the specified service period. In addition, comparing the cases of
CONCLUSIONS
Based on real-time monitoring data from the SCADA system, this paper combines the ABAQUS finite element software for modeling and a new structural fatigue reliability analysis method that considers the stochastic process of exceeding the threshold duration. The fatigue reliability of the maximum stress at the upper flange of the foundation ring of the wind turbine structure under normal operating conditions was calculated. The main research work and conclusions are as follows.
(1) Under normal operating conditions, the wind speed time series of each tower section is calculated by wind speed exponential model, orthogonal expansion method of random pulsating wind field and number theory point selection method in number theory, and then the wind load time series of each tower section and blade is calculated using the wind load calculation formula of standard for design of high-rising structures and the momentum-leaf vein theory. The wind loads are determined based on the real-time wind speed data collected by the SCADA system, so it should be a more reliable result.
(2) Establish a simplified model in ABAQUS finite element software in line with the engineering profile. The reasonableness of the structural model of the wind turbine was first verified by modal analysis. Subsequently, the wind load is applied to the model for instantaneous modal dynamics analysis to obtain the structural stress time course. The results show that the maximum stress region of the foundation ring is located at the edge of the upper flange, which is consistent with the engineering reality.
(3) Fatigue reliability in the region of maximum stress in the base ring is calculated using a structural fatigue reliability analysis method that considers random processes’ crossing-threshold duration. The results are compared with those of the traditional method to demonstrate the superiority and reasonableness of the method that takes into account the calculation of crossing-threshold durations.
DECLARATIONS
Authors’ contributions
Conceptualization, methodology, supervision: Zhang Z
Formal analysis, writing-original draft preparation: Liu Y
Investigation, writing-review and editing: Li W
Availability of data and materials
The data are available from the corresponding author upon reasonable request.
Financial support and sponsorship
This work was jointly supported by the Talent Recruitment Project of Hunan Province, China (grant no. 2023TJ-Z17), National Natural Science Foundation of China (grant no. 52478130), Regional Scientific and Technological Cooperation and Exchange Project of Hunan Association for Science and Technology (2024SKX-KJ-09).
Conflicts of interest
All authors declared that there are no conflicts of interest.
Ethical approval and consent to participate
Not applicable.
Consent for publication
Not applicable.
Copyright
© The Author(s) 2024.
REFERENCES
1. de Azevedo HDM, Araújo AM, Bouchonneau N. A review of wind turbine bearing condition monitoring: state of the art and challenges. Renew Sustain Energy Rev 2016;56:368-79.
3. Yang W, Tavner PJ, Crabtree CJ, Wilkinson M. Cost-effective condition monitoring for wind turbines. IEEE Trans Ind Electron 2010;57:263-71.
4. Mcmillan D, Ault GW. Condition monitoring benefit for onshore wind turbines: sensitivity to operational parameters. IET Renew Power Gen 2008;2:60-72.
5. Meng D, Yang H, Yang S, et al. Kriging-assisted hybrid reliability design and optimization of offshore wind turbine support structure based on a portfolio allocation strategy. Ocean Eng 2024;295:116842.
6. Meng D, Yang S, Yang H, De Jesus AMP, Correia J, Zhu SP. Intelligent-inspired framework for fatigue reliability evaluation of offshore wind turbine support structures under hybrid uncertainty. Ocean Eng 2024;307:118213.
7. Meng D, Yang S, de Jesus AMP, Zhu SP. A novel kriging-model-assisted reliability-based multidisciplinary design optimization strategy and its application in the offshore wind turbine tower. Renew Energy 2023;203:407-20.
8. Meng DB, Zhu SP. Multidisciplinary design optimization of complex structures under uncertainty. Boca Raton: CRC Press; 2024.
9. Nilsson J, Bertling L. Maintenance management of wind power systems using condition monitoring systems - life cycle cost analysis for two case studies. IEEE Trans On Energy Conver 2007;22:223-9.
10. Kusiak A, Verma A. A data-driven approach for monitoring blade pitch faults in wind turbines. IEEE Trans Sustain Energy 2010;2:87-96.
11. Gill S, Stephen B, Galloway S. Wind turbine condition assessment through power curve copula modeling. IEEE Trans Sustain Energy 2012;3:94-101.
12. Kusiak A, Verma A. Monitoring wind farms with performance curves. IEEE Trans Sustain Energy 2013;4:192-9.
13. Zaher A, Mcarthur SDJ, Infield DG, Patel Y. Online wind turbine fault detection through automated SCADA data analysis. Wind Energy 2009;12:574-93.
14. Garcia MC, Sanz-Bobi MA, del Pico J. SIMAP: intelligent system for predictive maintenance: application to the health condition monitoring of a windturbine gearbox. Comput Ind 2006;57:552-68.
15. Yang W, Court R, Jiang J. Wind turbine condition monitoring by the approach of SCADA data analysis. Renew Energy 2013;53:365-76.
16. Zhang S, Lang ZQ. SCADA-data-based wind turbine fault detection: a dynamic model sensor method. Control Eng Pract 2020;102:104546.
17. Zhang F, Wen Z, Liu D, Jiao J, Wan H, Zeng B. Calculation and analysis of wind turbine health monitoring indicators based on the relationships with SCADA data. Appl Sci 2020;10:410.
18. Tang M, Chen W, Zhao Q, et al. Development of an SVR model for the fault diagnosis of large-scale doubly-fed wind turbines using SCADA data. Energies 2019;12:3396.
19. Liu X, Du J, Ye ZS. A Condition monitoring and fault isolation system for wind turbine based on SCADA data. IEEE Trans Ind Inf 2022;18:986-95.
20. Velarde J, Mankar A, Kramhøft C, Sørensen JD. Probabilistic calibration of fatigue safety factors for offshore wind turbine concrete structures. Eng Struct 2020;222:111090.
21. Wang K, Ji C, Xue H, Tang W. Fatigue damage characteristics of a semisubmersible-type floating offshore wind turbine at tower base. J Renew Sustain Energy 2016;8:053307.
22. Fu B, Zhao J, Li B, et al. Fatigue reliability analysis of wind turbine tower under random wind load. Struct Saf 2020;87:101982.
23. Zhu D, Ding Z, Huang X, Li X. Probabilistic modeling for long-term fatigue reliability of wind turbines based on Markov model and subset simulation. Int J Fatigue 2023;173:107685.
24. Li M, Luo Y, Xie L, Tong C, Chen C. Fatigue reliability assessment method for wind power gear system based on multidimensional finite element method. J Risk Reliab 2024;238:540-58.
25. Liu Z, He Z, Tu L, Liu X, Liu H, Liang J. A fatigue reliability assessment approach for wind turbine blades based on continuous time Bayesian network and FEA. Qual Reliab Eng 2023;39:1603-21.
26. Horn JT, Leira BJ. Fatigue reliability assessment of offshore wind turbines with stochastic availability. Reliab Eng Syst Saf 2019;191:106550.
27. Liu G, Liu H, Zhu C, Mao T, Hu G. Design optimization of a wind turbine gear transmission based on fatigue reliability sensitivity. Front Mech Eng 2021;16:61-79.
28. Zhang Z, Zhou M, Fang M. First-passage probability analysis of Wiener process using different methods and its applications in the evaluation of structural durability degradation. Eur J Environ Civ Eng 2021;25:1763-81.
29. Roberts JB. First-passage probabilities for randomly excited systems: diffusion methods. Probabilist Eng Mech 1986;1:66-81.
30. Zhang Z, Liu M, Zhou M, Chen J. Dynamic reliability analysis of nonlinear structures using a Duffing-system-based equivalent nonlinear system method. Int J Approx Reason 2020;126:84-97.
31. Pastorcic D, Vukelic G, Bozic Z. Coil spring failure and fatigue analysis. Eng Fail Anal 2019;99:310-8.
32. Weibring M, Gondecki L, Tenberge P. Simulation of fatigue failure on tooth flanks in consideration of pitting initiation and growth. Tribol Int 2019;131:299-307.
33. Zhang Z, Liu X, Zhang Y, Zhou M, Chen J. Time interval of multiple crossings of the Wiener process and a fixed threshold in engineering. Mech Syst Signal Proc 2020;135:106389.
34. Zhang Z, Zhao C, Zhao Z, Wang F, Zhao B. Structural fatigue reliability evaluation based on probability analysis of the number of zero-crossings of stochastic response process. Eng Fail Anal 2023;143:106923.
35. Liu G, Gao K, Law SS. An improved sieve point method for the reliability analysis of structures. Probabilist Eng Mech 2020;62:103087.
36. National Standard of the People’s Republic of China. Standard for design of high-rising structures (GB50135-2019). Beijing: China Architecture Industry Press; 2019. Available from: https://www.gbstandards.org/GB_standard_english_3.asp?code=GB%2050135-2019&id=45634 [Last accessed on 26 Sep 2024].
37. Gao K, Liu G, Tang W. High-dimensional reliability analysis based on the improved number-theoretical method. Appl Math Model 2022;107:151-64.
38. Niu Q. New energy technologies-wind energy technology. Beijing: Science Press; 2009. Available from: https://ss.zhizhen.com/detail_38502727e7500f268a9ccc00f75bb01ccfc384332d18b1e11921b0a3ea25510134114c969f2eae5c8619c3781aeff6c1ed60753c1335db4b2ac4765c2ca0e502d2822a9bb48c12c32752f14c8ebc102a [Last accessed on 26 Sep 2024].
39. National Standard of the People’s Republic of China. Standard for design of steel structures (GB 50017-2017). Beijing: China Architecture & Building Press; 2017. Available from: https://www.chinesestandard.net/PDF.aspx/GB50017-2017 [Last accessed on 26 Sep 2024].
Cite This Article
How to Cite
Download Citation
Export Citation File:
Type of Import
Tips on Downloading Citation
Citation Manager File Format
Type of Import
Direct Import: When the Direct Import option is selected (the default state), a dialogue box will give you the option to Save or Open the downloaded citation data. Choosing Open will either launch your citation manager or give you a choice of applications with which to use the metadata. The Save option saves the file locally for later use.
Indirect Import: When the Indirect Import option is selected, the metadata is displayed and may be copied and pasted as needed.
About This Article
Copyright
Data & Comments
Data
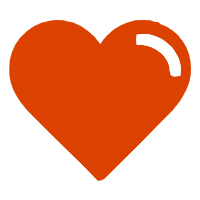
Comments
Comments must be written in English. Spam, offensive content, impersonation, and private information will not be permitted. If any comment is reported and identified as inappropriate content by OAE staff, the comment will be removed without notice. If you have any queries or need any help, please contact us at support@oaepublish.com.